The main parameters of plywood and other sheet materials such as construction templates can be divided into three aspects.
Face veneer: This is the surface layer of the board, usually made of high-quality wood or other materials. The quality and appearance of the face veneer directly affect the overall aesthetics and strength of the board.
Core veneer: The core veneer is located between the face veneers and is typically made of cheaper wood or other materials. The quality and density of the core veneer can affect the strength and stability of the board.
Adhesive: The adhesive is a crucial component that bonds the face veneers and core veneer together. Different types of adhesives have different characteristics, such as water resistance, fire resistance, and weather resistance. Choosing the appropriate adhesive can enhance the durability and lifespan of the board.
Using different materials for these three aspects for different usage areas.
Face Veneer
Plywood is used for different purposes based on the different face veneers used.
1. Commercial plywood: The face veneer of commercial plywood is mainly made of precious wood species, such as Okouma (subject to a 66% anti-dumping tariff by the UK), Bintangor, Pencil Cedar, Radiate Pine (from New Zealand), Birch, or even Poplar. These veneers are sourced from African and other regions and are typically rotary-cut to showcase their beautiful colors and grain patterns. The attached images provide examples and descriptions.
The image can be enlarged. The image above shows Okouma, a fine-grained wood species. The UK imposed anti-dumping measures on Okouma about 20 years ago, which effectively restricted its importation. Okouma is sourced from Gabon in Africa and takes hundreds of years to mature, leading to protests from environmental organizations and subsequent anti-dumping actions.
The substitute for Okouma is a similar-colored wood called Bintangor. The market primarily offers a thickness of 0.2mm for the face and back veneers, which can be customized up to 0.3mm. The standard grade is BB/CC, with the face veneer being BC and the inner veneer being BC. However, in practice, the product usually maintains a surface grade of B/C. B-grade may have slight color variations, while C-grade allows for small knots, no larger than the size of a pound coin, and up to three dead knots that can be patched or filled. It is common knowledge that due to the thinner face veneer, the price difference between C and D grades is not significant.
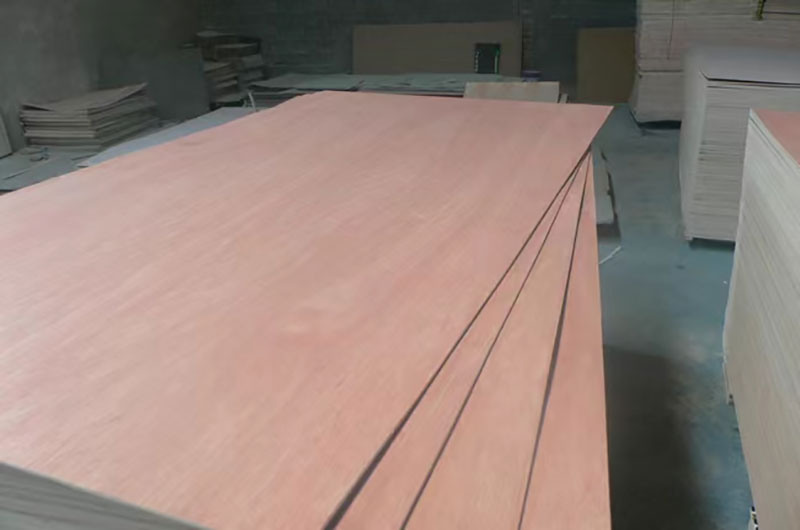
Bintangor has a reddish color and coarser longitudinal fibers compared to Okouma. Its cross-grain fibers are relatively weaker than Okouma. Bintangor does not match the smoothness of Okouma. It is considered a substitute product for Okouma.
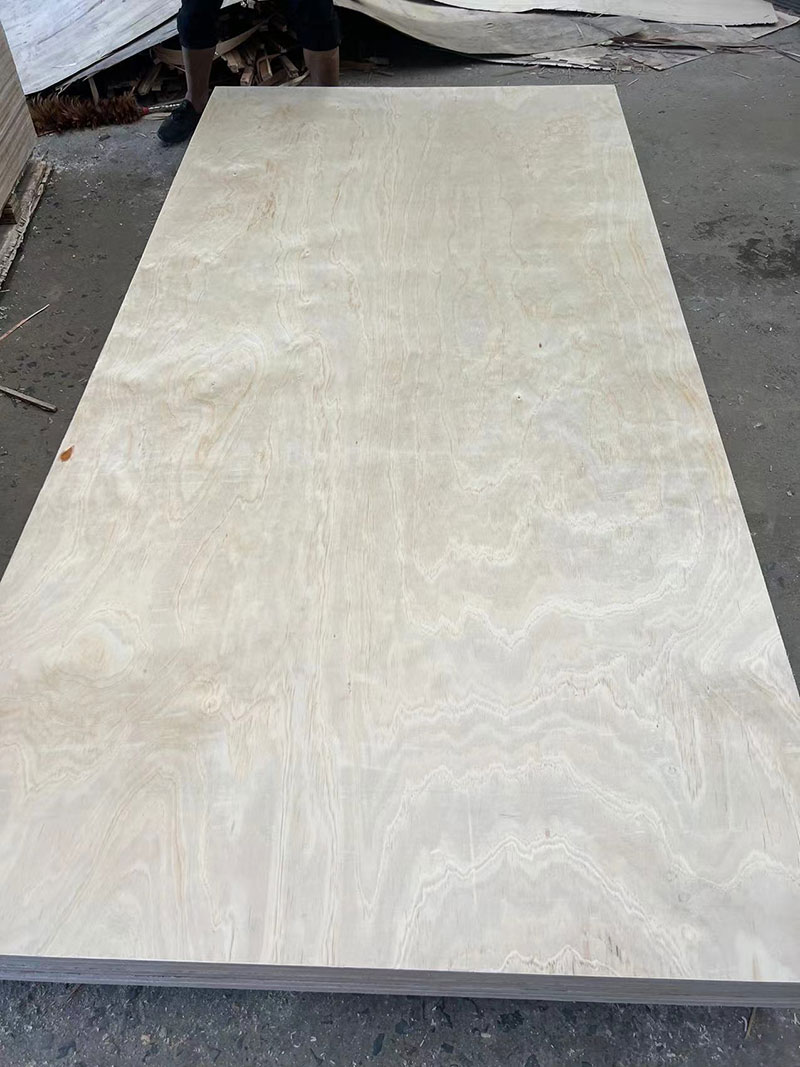
Radiata pine (from New Zealand) is the main source of pine wood. Due to the coarser longitudinal fibers of larch and camphor pine, they are difficult to rotary cut and are usually used as lumber. Because radiata pine has many knots, the basic market grade is C/D grade. The normal thickness of radiata pine is around 0.5mm.
Birch wood is mainly produced in Russia and China, with the main consumer markets being Europe and the United States. The grading standards for birch wood are different from the British system, with grades such as C+/C, BB/CP, and so on. The disadvantage is that the grade is not high, with the conventional grades being C+ and C. The sizes are usually 5x5 or 5x10, and so on.
The advantage of poplar wood is that it has a relatively high grade. The conventional grade can be B/C, and special requirements can achieve a pure white grade of A. The picture below is from a door factory in Portugal. The AA grade is pure white. This is poplar wood that has been bleached with hydrogen peroxide. Most factories are reluctant to produce bleached poplar wood because it can easily damage the machinery.
The above introduction was about natural wood veneer, now let's introduce some artificial wood veneers.
Engineered veneer (EV) currently holds over half of the market share. In the early stages, some precious woods such as black walnut and teak were used, resulting in higher prices and varying quality. Later on, the color of the wood was altered through boiling, and Italian craftsmen began dyeing poplar wood. Poplar wood was sliced into 0.7mm thin pieces, dyed, and then laminated to create veneer. Finally, the veneer was sliced at a 45-degree angle, resulting in EV veneer with different colors and patterns, imitating various precious woods. Since the raw material is still wood, the variety of colors is also diverse. Please refer to the images below.
The above mentioned were all wood-based substrates. Now, let's introduce the surface layer as panel material. Of course, the usage varies depending on the material.
a. Film faced plywood,The main process involves applying waterproof glue on the paper (in black and brown colors).
Of course, the surface can also be pressed with various patterns using steel plates. For example, the anti-slip board shown in the picture, wireless or anti-slip film faced plywood (sometimes using double-layer film paper). Brown panels are mainly used for construction templates and are the preferred products for construction templates in the UK. Cheaper options are also available in black. The main indicator for construction templates is the number of uses. In addition to brown or black film paper, different adhesives are used internally to enhance waterproof performance. The details will be explained when discussing adhesives later. The best wood and adhesive, combined with brown film paper, can be used up to 50 times (there is a difference between domestically produced 250g/m2 and Finnish Thule, 125g/m2 film paper). As for construction templates, there are also other options, such as MDO (more commonly used in Ireland) (Spanish templates are special products). The picture below shows MDO.MDO is claimed to be able to be used 50 times, and 1220x2440 is the standard size.
Anti-slip boards is small market share products primarily used for stage platforms (dance stages), horse stables (in Europe, where frequent cleaning and slip resistance are required), bus and truck flooring (for vehicle modification in the UK), and accessories for small trailers (as shown in the comparison picture of handles in German building material supermarkets).
Of course, we can customize the anti-slip boards according to customer requirements, including special dimensions and hole punching. Currently, our standard sizes for coated boards are 1220x2440 (UK), 1250x2500 (Europe), 1500x3000 (Europe), 1525x3150, and so on.
However, there is also around 10% of the market for other products in construction formwork, such as green and yellow boards, which are used more frequently and have higher prices, but their market acceptance is not high.
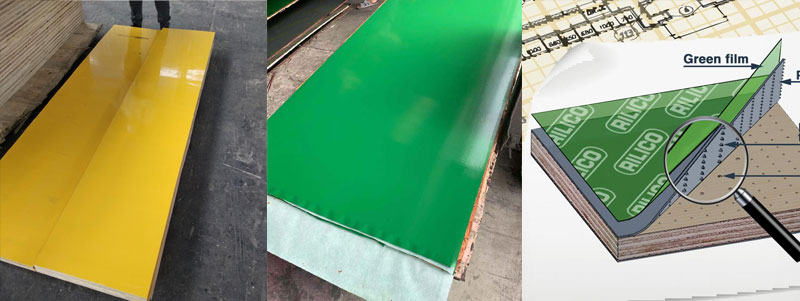
The film paper used in construction formwork is made from phenolic adhesive. Phenolic adhesive has strong waterproof properties, and phenolic plywood can be boiled in water for 36-72 hours without delamination. It is mainly used for outdoor applications because phenol is toxic.
Melamine-faced boards are mainly used for decoration purposes and can be provided in different colors.
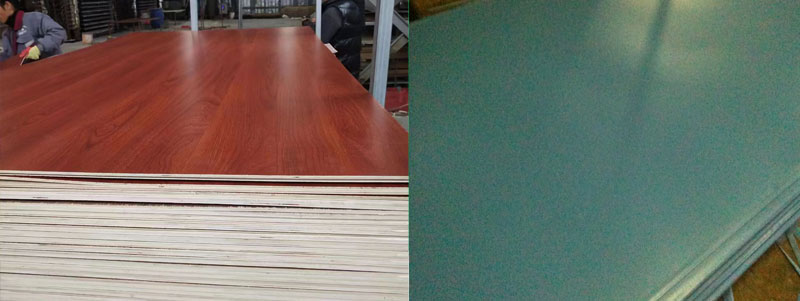
Of course, these can be provided with sample cards, and customers can choose based on the sample cards.
HPL (High-Pressure Laminate) is the preferred choice in the Israeli market, available in pure white, various colors, and embossed patterns.

Glue:
The main types of adhesives used in the plywood market include:
1. MR-Urea formaldehyde adhesive. This adhesive is gradually being phased out of the market. It is a glue made from the reaction of formaldehyde and urea. Its main characteristic is a high formaldehyde content, which is rejected by most markets except for a few that do not have strict formaldehyde regulations.
2. Melamine formaldehyde adhesive. This adhesive is based on urea formaldehyde adhesive, with the addition of melamine to achieve a series of reversible reactions that reduce formaldehyde content. All the adhesives used in the European market, such as E2 and E1, are melamine formaldehyde adhesives. The plywood made with this adhesive can withstand boiling in water for 6-8 hours. The standard melamine content is usually measured by boiling in water for 8 hours. Melamine formaldehyde adhesive has properties such as moisture resistance and termite resistance, making it the preferred adhesive for indoor decoration.
3. Phenol formaldehyde adhesive. This adhesive is a product of the reaction between phenol and formaldehyde, and it is mainly used for outdoor waterproofing. Phenol formaldehyde resin plywood can withstand boiling in water for over 36 hours (for domestic products) or up to 72 hours (for products like Taier adhesive). It is expensive and has toxic characteristics. It is primarily used for construction formwork. However, due to intense market competition, WBP adhesive, which used to be called phenol formaldehyde adhesive, is now also referred to as melamine formaldehyde adhesive or WBP (water boiling proof) adhesive.
4. Formaldehyde-free adhesive.
Soy-based adhesive, as well as Japanese adhesive, are specific cases that require special discussion.
The requirements for adhesives in the European Union and the United Kingdom are categorized as E1, E2, etc. For E2, the formaldehyde emission level is 5.5 milligrams per cubic meter, while for E1, it is 1.5 milligrams per cubic meter. In the United States, California has introduced the E0 standard, with a formaldehyde emission level of 0.5 milligrams per cubic meter. In the Japanese market, the corresponding categories for plywood adhesives are F1-F4, where F4 is equivalent to E0 and F3 is equivalent to E1. The Australian market has a specific requirement of F18 for construction templates. If there are any questions regarding these various adhesive types, discussions can be conducted on topics such as chemistry, processing, and chemical reactions.
Core Veneer:
The core board is referred to as internal layers, medium board, etc.
This type of core board, which consists of four pieces joined together to form a complete board, is typically used in the inner layers of high-grade boards, particularly those near the surface.
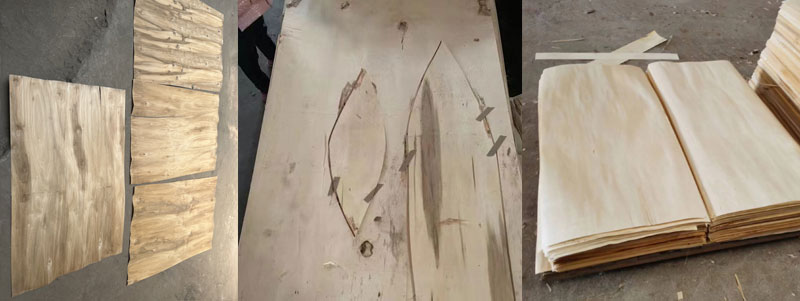
According to the variety classification:
Currently, core boards in the market are basically divided into three varieties.
Poplar wood: Poplar wood has a short growth cycle of 5-7 years and has advantages such as soft texture, fewer knots, and thick diameter. After being compressed into plywood, its density is around 580. The normal moisture content of plywood is around 12%.
Hardwood or mixed wood: Mainly eucalyptus wood, which is characterized by its dark color and density of around 650. After compression, it has a higher hardness ratio. Eucalyptus wood is also considered a fast-growing wood. However, its disadvantage is that it has a thin diameter and more knots. The time to reach maturity is about 5 years. It is mainly used in construction templates and other products.
Birch wood: Main production areas include Russia and some regions in China. The main markets are the United States and Europe. Recently, the birch plywood market has been disrupted due to the Russia-Ukraine war.
Level:
According to the pictures above, it can be divided into panels and repair of large and small holes. The grade of the internal core board determines the specific surface smoothness. For example, when making furniture or using cutting boards, it is necessary to control the overlap and number of layers away from the core. Top-grade plywood needs to be machine-spliced into a whole sheet to avoid small pieces being spliced into a whole. The following pictures introduce the splicing methods to achieve a whole sheet for each layer and reduce overlap and distance from the core.
Processing can be classified into manual and machine splicing, etc.
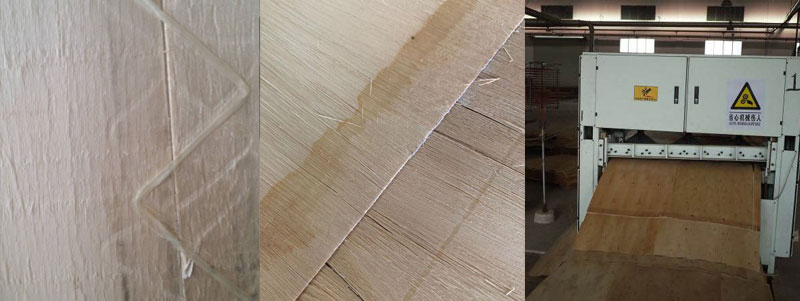
The above provides a brief introduction to plywood based on its material. Later, we will provide some photos to enhance understanding and differentiation of the products.